Blog
Die richtige Oberflächenvorbereitung – Tipps und Tricks für ein makelloses Endergebnis
Die richtige Oberflächenvorbereitung gewährleistet eine gute Haftung, Glätte und eine langlebige Endbeschichtung unter Berücksichtigung der wesentlichen Schritte.
Die richtige Oberflächenvorbereitung ist die Grundlage jedes Lackierprojekts und der Schlüssel zu einer langlebigen sowie optisch perfekten Beschichtung. Eine unsachgemäße Vorbereitung kann zu schlechter Haftung der nachfolgenden Schichten, sichtbaren Kratzern und anderen Mängeln führen, die das Endergebnis beeinträchtigen. Im Folgenden finden Sie die wichtigsten Schritte, um eine optimale Oberflächenvorbereitung zu erreichen.
Saubere und trockene Oberfläche
Vor Beginn der Arbeiten muss die Oberfläche vollkommen sauber, trocken sowie frei von Staub, Feuchtigkeit und Fett sein. Verunreinigungen, die durch den Arbeitsprozess entstehen, sollten mit einem Anti-Silikon-Reiniger wie 9515 Anti-Sil entfernt werden. Dadurch wird eine optimale Haftung der folgenden Beschichtungen gewährleistet und potenzielle Probleme in späteren Arbeitsschritten vermieden.
Spachteln – richtiges Mischen und Auftragen
Beim Spachteln ist es wichtig, den Spachtel richtig zu mischen und aufzutragen. Überschüssiges Harz darf nicht in die Spachtelmasse eingerührt, sondern muss abgegossen werden. Wenn eine Temperaturkontrolle nicht möglich ist, sollte auf IR- oder andere Hochtemperatur-Trocknungsmethoden verzichtet werden, da die maximale Trocknungstemperatur für Polyester-Spachtel 45°C beträgt. Eine erzwungene Trocknung kann Haftungsprobleme verursachen.
Der Härteranteil liegt zwischen 2 % und 3 % – im Sommer 2 %, im Winter 3 %. Für hohe Temperaturen und große Flächen wird der langsame Härter 6067 Polyester Putty Hardener, Slow empfohlen. Um eine präzise Dosierung zu gewährleisten, ist der 5920 Putty Dispenser ideal, da er eine Anpassung an verschiedene Temperaturbedingungen ermöglicht. Zur genauen Dosierung des Härters kann auch eine Präzisionswaage verwendet werden. Eine Überdosierung des Härters kann zu Peroxid-Blutungen führen.
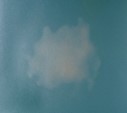
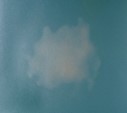
Das Mischen sollte so lange erfolgen, bis keine Spuren des Härters mehr sichtbar sind (rote oder blaue Flecken). Vor jeder neuen Schicht müssen eventuelle Kratzer entfernt werden, um eine gleichmäßige Oberfläche zu gewährleisten. Tragen Sie den Spachtel in mehreren dünnen Schichten auf, da eine dicke Schicht zu Unebenheiten führen kann.
Ein Kontrollpuder wie 3530 Dry Guide Coat ist vor dem Schleifen entscheidend, da es kleine Löcher und Unebenheiten sichtbar macht, die vor dem Auftrag der Grundierung beseitigt werden müssen. Schließen Sie die Spachtelmasse nach jeder Benutzung gut, um ein Austrocknen zu vermeiden.
Schleifen – die richtige Wahl der Körnung
Vermeiden Sie grobe Schleifpapiere wie P60 oder P80, da sie zu tiefen Kratzern führen, die schwer zu entfernen sind. Da Spachtel hygroskopisch ist, muss trockengeschliffen werden.
Beginnen Sie mit einer P120-Körnung und arbeiten Sie sich schrittweise nach oben, wobei der Sprung zwischen den Körnungen nicht mehr als 100 betragen sollte (z. B. P120, P150, P180, P240, P320). Beim Wechsel zu einer feineren Körnung achten Sie darauf, dass alle Kratzer der vorherigen Körnung entfernt wurden, da die nächste Körnung diese nicht korrigieren kann. Diese Methode ermöglicht eine glatte und gleichmäßige Oberflächenvorbereitung vor dem Auftragen der Grundierung.
Auftragen und Schleifen von Füller/Grundierung
Beim Auftragen der Grundierung ist es wichtig, dass zwischen den Schichten eine Ablüftzeit bis zum matten Erscheinungsbild eingehalten wird. Mehrere dünne Schichten sorgen für eine bessere Isolation und bilden eine Schutzschicht, die das Risiko von Reaktionen mit vorherigen Schichten verringert.
Falls die Spachtelarbeit mit P240 abgeschlossen wurde, beginnen Sie beim Schleifen der Grundierung mit P320 und wechseln Sie dann zu P400. Verwenden Sie hierbei ein Schleifpapier mit weicher Zwischenschicht, z. B. 4630 Soft Interface Pad. Bei empfindlichen Farben (Perlmutt, Xirallic) ist eine abschließende Schleifung mit P500 oder P600 erforderlich. Die ideale Werkstatttemperatur liegt bei mindestens 15°C, da niedrigere Temperaturen die Trockenzeiten negativ beeinflussen können.
Große blanke Metallflächen müssen vor dem Auftragen der Füller mit einer geeigneten Grundierung (Epoxy, Etch) geschützt werden.
Richtige Anwendung von Härtern und Verdünnungen
Beachten Sie stets die technischen Datenblätter (TDS) bei der Verwendung von Härtern und Verdünnungen. Unsere Produktetiketten sind mit QR-Codes versehen, die einen einfachen Zugriff auf die technischen Dokumente ermöglichen. Alle Dokumente sind auch unter Technische und Sicherheitsdokumentation abrufbar.
Vor dem Hinzufügen von Verdünnung muss der Härter gut in das Füllmaterial eingerührt werden, um eine gleichmäßige chemische Reaktion zu gewährleisten. Nitro-Verdünnung darf nur zur Reinigung der Werkzeuge verwendet werden.
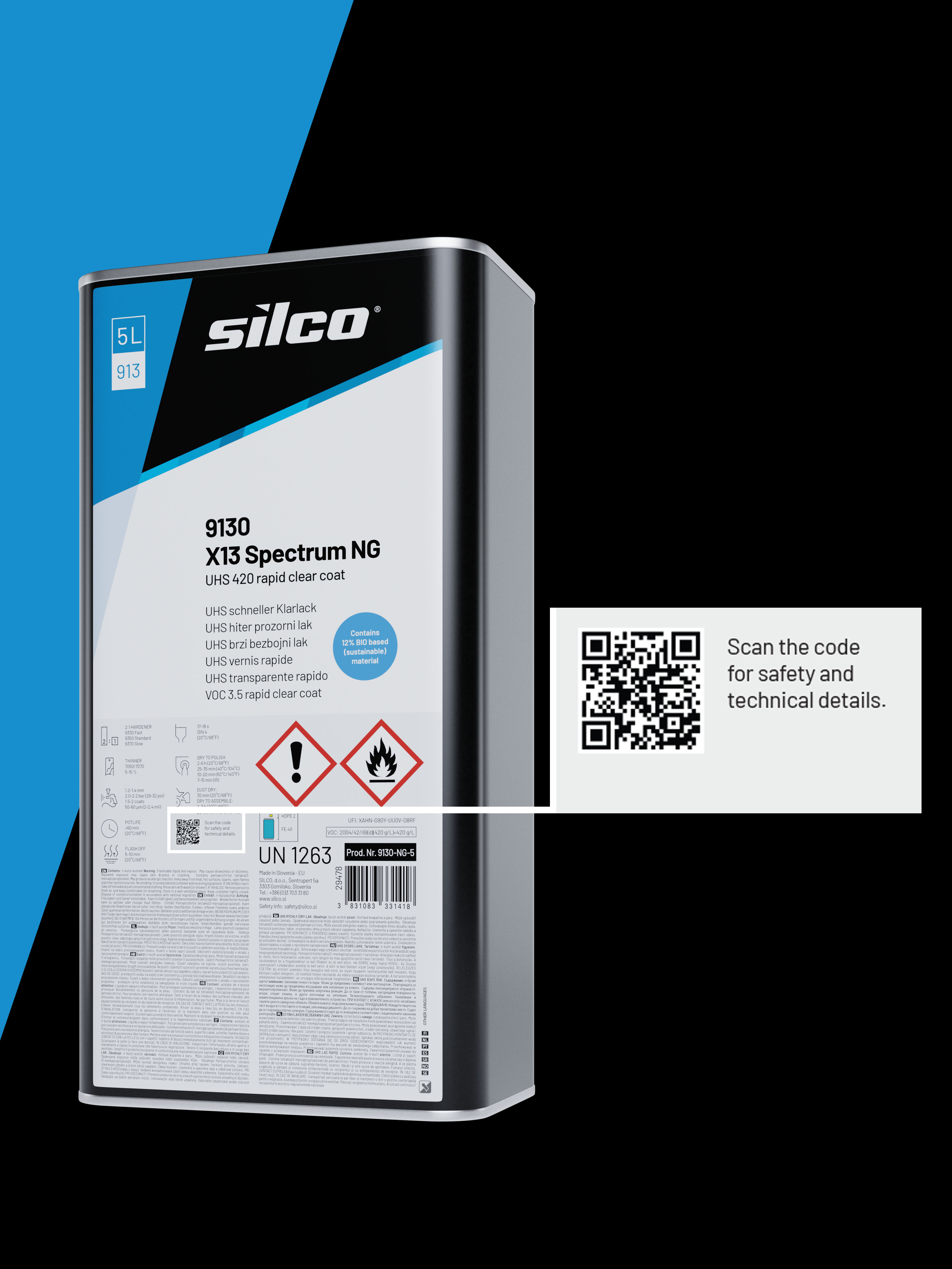
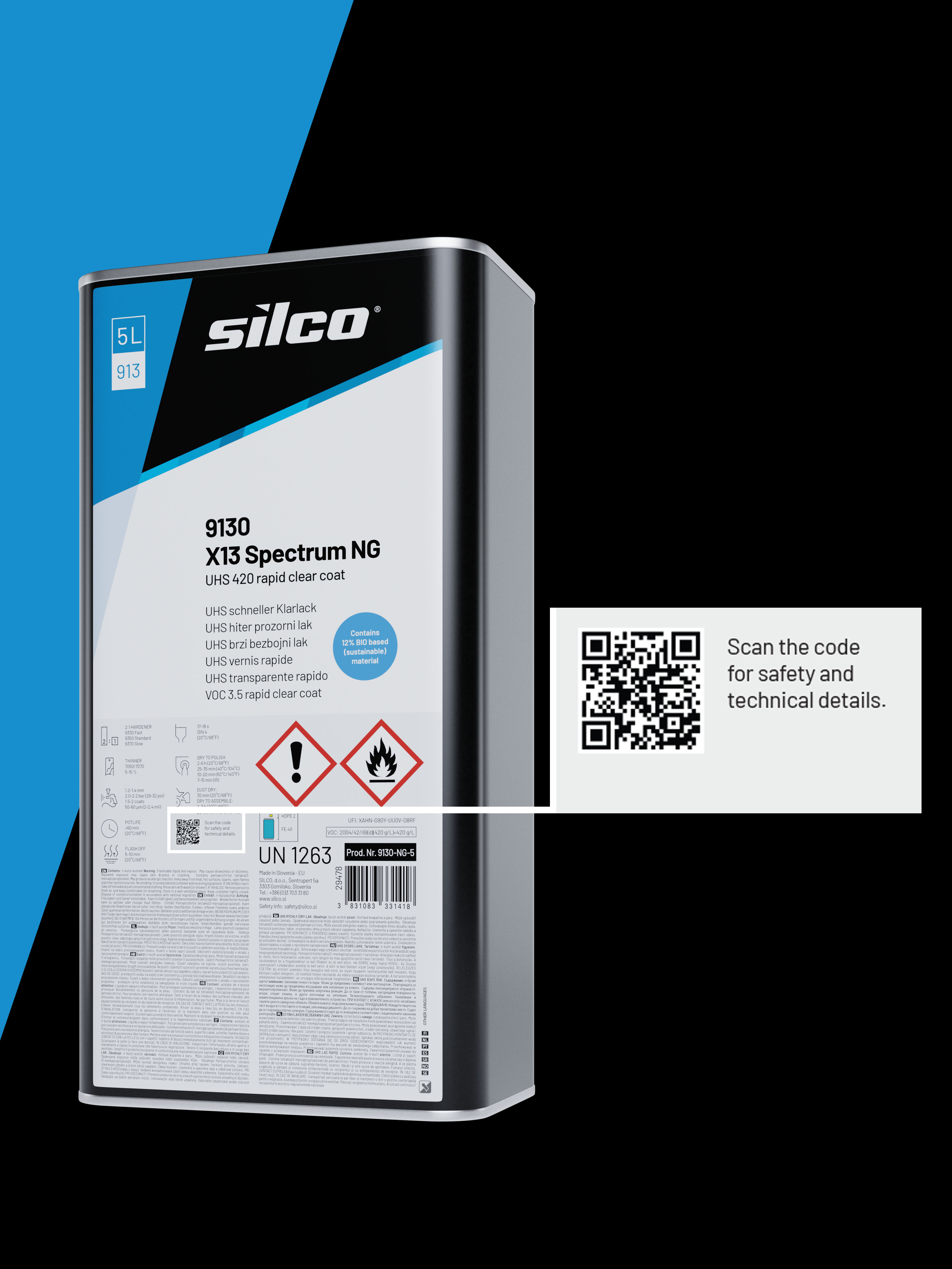
Spritzpistole und Druckeinstellung
Wählen Sie für das Auftragen der Grundierung die geeignete Spritzpistole. Je nach Reparaturart wird eine Düsengröße von 1,4 mm bis 1,8 mm empfohlen. Der Arbeitsdruck liegt zwischen 1,5 und 2 bar. Nach jeder Anwendung muss die Spritzpistole mit einem geeigneten Reiniger wie 5555 Nitro Thinner gereinigt werden.
Lackierraum und Belüftung
Die Grundierung sollte in einem Raum mit ausreichender Belüftung und Filtration aufgetragen werden. Eine gute Belüftung ist entscheidend für eine schnelle und gleichmäßige Trocknung der Beschichtung. Es ist ratsam, die Grundierung von größeren zu kleineren Flächen hin aufzutragen, um das Überlappen von Overspray an den Kanten der vorherigen Schicht zu vermeiden.
Fazit
Die richtige Oberflächenvorbereitung ist nicht nur ein technischer Schritt, sondern entscheidend für ein makelloses und langlebiges Endergebnis. Durch die konsequente Einhaltung aller oben genannten Richtlinien – von der Reinigung über das korrekte Spachteln und Schleifen bis hin zur richtigen Verwendung von Härtern, Verdünnungen und Lackiergeräten – stellen Sie sicher, dass Ihr Projekt erfolgreich und optisch perfekt wird. Sorgfalt und Detailgenauigkeit sind entscheidend, denn eine gut vorbereitete Oberfläche ist die Basis für eine makellose Endlackierung, die sowohl Sie als auch Ihre Kunden begeistert.